Materiali e metodi costruttivi rivoluzionari e batterie e motori sempre più piccoli: così si riduce il peso delle auto a zero emissioni
.
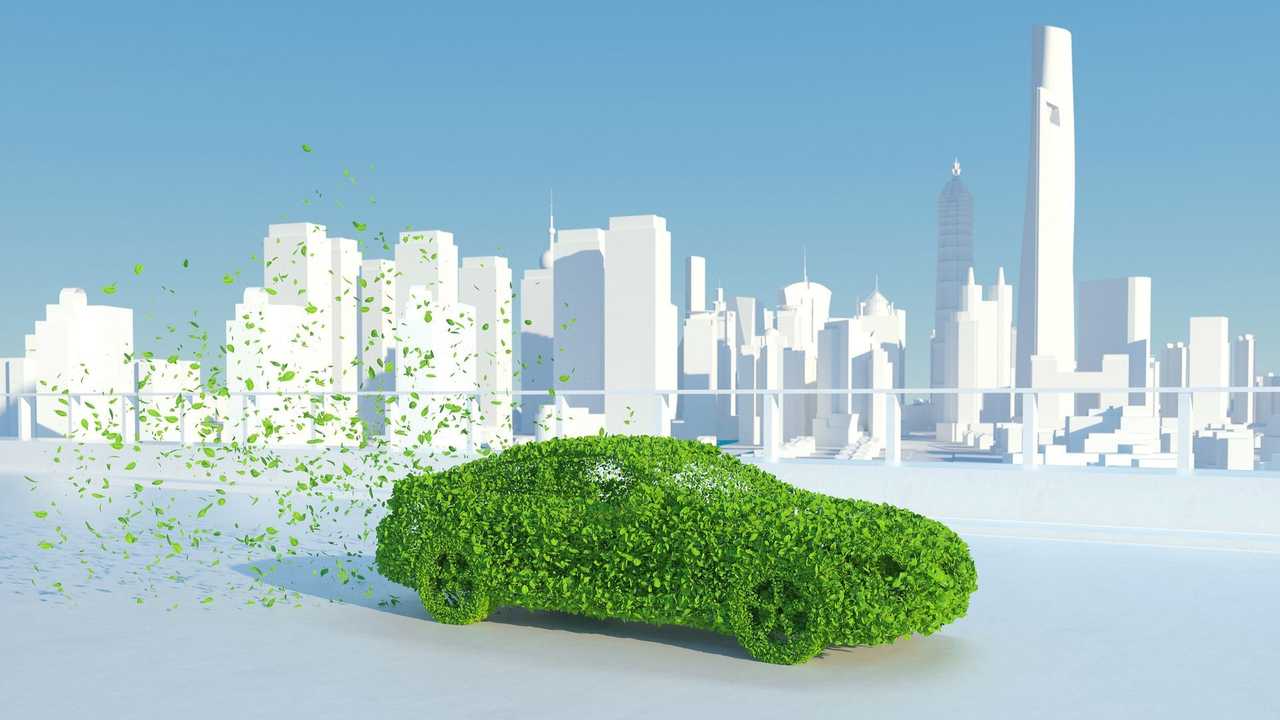
Auto elettrica vuol dire leggerezza. O meglio: ricerca della leggerezza. Così, un po’ per i naturali progressi tecnologici in termini di leghe metalliche e materiali compositi, un po’ per il fatto che con l’avvento delle vetture a batteria la riduzione del peso è diventata una priorità, l’industria sta facendo grossi passi avanti sotto diversi punti di vista.
Tutto, chiaramente, per migliorare l’efficienza energetica e aumentare le percorrenze. Un po’ come accade anche sul fronte dell’aerodinamica, che proprio con l’auto elettrica ha fatto consistenti passi in avanti. Ma torniamo a parlare di chilogrammi.
Leggerezza stampata in 3D
La situazione attuale, in termini di riduzione del peso, è nota. Acciai altoresistenziali, fibra di carbonio e resine di qualsiasi foggia permettono di ridurre le masse delle auto. In questo senso, i ricercatori della Oak Ridge National Laboratory hanno scoperto un fenomeno chiamato “rimescolamento del carico” che interessa le leghe metalliche.
Scendendo nel dettaglio dello studio, i ricercatori hanno scoperto attraverso la diffrazione neutronica – metodo utilizzato per determinare la struttura atomica di un materiale – che una lega metallica sottoposta a stress, trasferisce una parte del carico su aree diverse rispetto a quella dove viene applicata la forza. Questo significa che rinforzare una zona “nevralgica” di una componente può non renderlo più resistente proprio a causa del fatto che il componente stesso potrebbe danneggiarsi da un’altra parte.
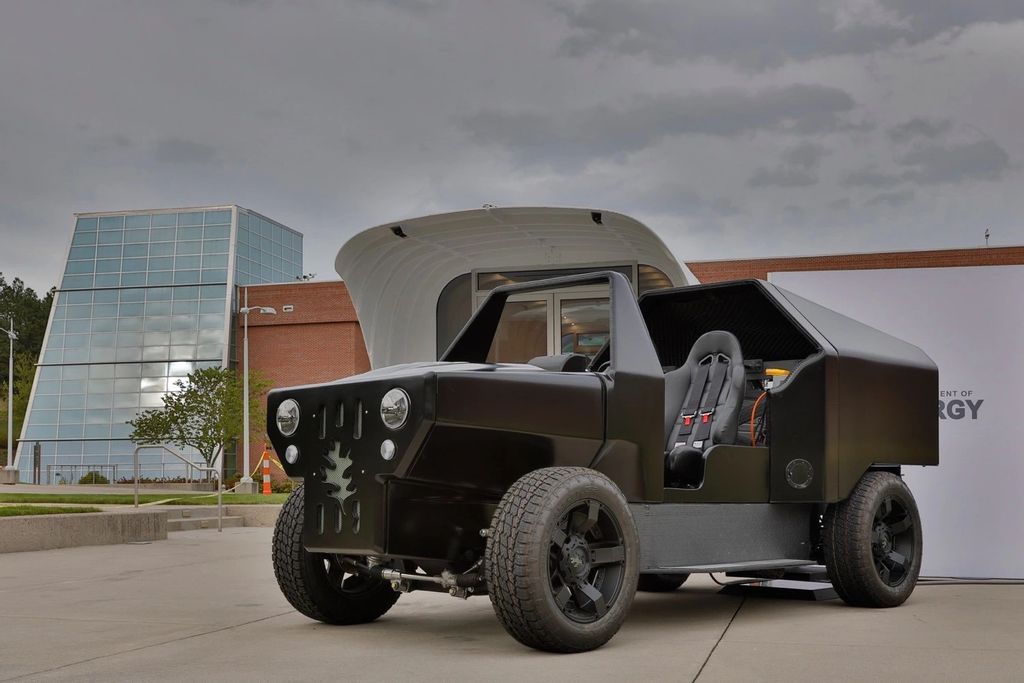
Un prototipo di auto elettrica stampato in 3D dai laboratori Oak Ridge
Ora, quindi, stanno valutando metodi rivoluzionari di stampa 3D che consentano di rinforzare meno le zone direttamente sottoposte a stress e di intervenire invece in altri punti dove le forze vanno a scaricarsi. Questo metodo consentirà di realizzare componenti dotati di pari resistenza ma di minore peso, con evidenti vantaggi sulla massa finale di una vettura.
Auto più leggere con le Giga Press
In attesa di vedere questi metodi diffondersi tra le Case automobilistiche, c’è chi ha trovato comunque il modo di risparmiare peso sulle sue auto elettriche. È Elon Musk, che stampando le scocche delle sue auto (per ora, a dire il vero, solo della Model Y, ma presto anche del Cybertruck), riduce drasticamente i pezzi necessari per lo scheletro dell’auto e di giunture e saldature che si traducono anche in meno kg di metallo da portare a spasso.
Il metodo, come è noto, è reso possibile grazie all’adozione delle Giga Press: enormi presse che arrivano a 9.000 tonnellate e che sono prodotte dall’italiana Idra. Per ora questa tecnica è usata solo da Tesla, ma tante Case stanno cercando di accaparrarsi macchinari simili per risparmiare tempo, soldi e materiali.
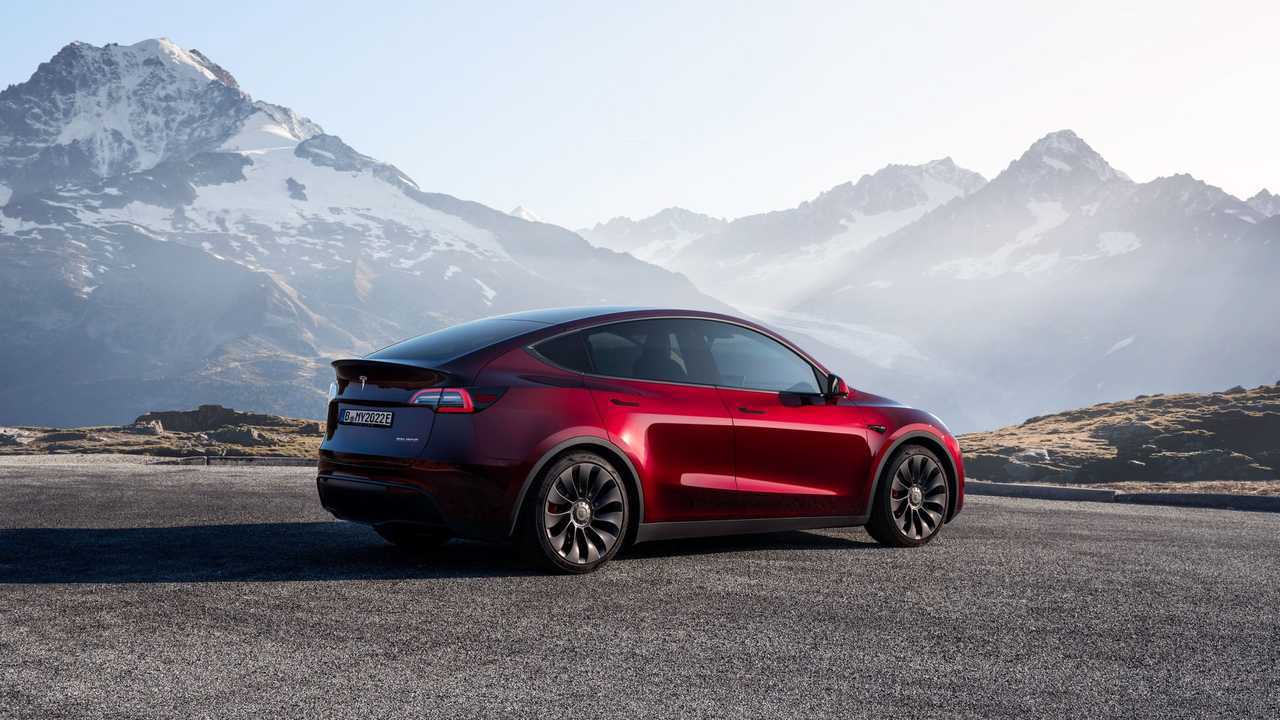
Una Tesla Model Y, prima auto con il retro della scocca stampato con le Giga Press
Il nodo batterie
Se c’è una cosa che aumenta il peso delle auto elettriche, sono le batterie. Per capirci, una batteria da 100 kWh (quella di una vettura elettrica di grosse dimensioni) può arrivare a pesare 550-600 kg. Conseguentemente, una batteria da 50 kWh può arrivare a 250-300 kg. Facciamo un esempio concreto: la Fiat 500 elettrica pesa esattamente 385 kg della Fiat 500 1.0 benzina mild Hybrid. D’accordo, sono due auto diverse sotto diversi punti di vista, ma il dato dà l’idea del problema.
Le Case, per risolverlo, si muovono principalmente in due direzioni. La prima riguarda l’architettura generale della batteria, la seconda le singole celle. Partiamo proprio dalle celle: cambiare la composizione chimica e la struttura interna delle celle permette di aumentare la densità energetica, con la conseguenza che ne serviranno meno per immagazzinare la stessa quantità di energia e mantenere invariati i dati sulle autonomie.
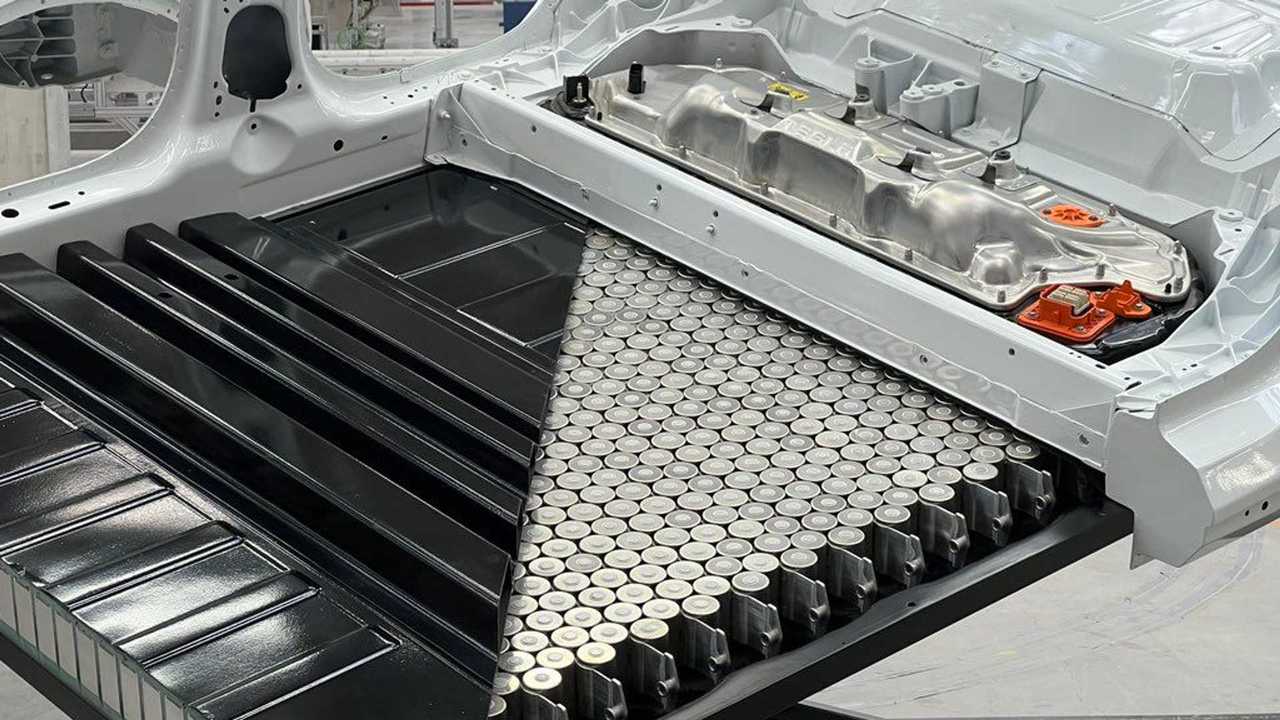
Un pacco batteria con architettura cell-to-pack
Poi, come detto, c’è la batteria nel suo complesso. Qui le mosse sono diverse. Ultimamente si sta diffondendo la soluzione cell-to-pack, che elimina la componente intermedia dei moduli e permette cosi di aumentare la percentuale “attiva” all’interno del pacco. E poi c’è la soluzione della batteria strutturale (chiamata anche cell-to-chassis), con la batteria che va a sostituirsi a una parte della scocca e permette di risparmiare a livello di telaio.
Migliorano anche i motori
Altra componente sulla quale si lavora per ridurre pesi e ingombri sono i motori. In questo senso, startup come Yasa o Magnax stanno lavorando a nuove unità a flusso assiale che riescono a garantire maggiori prestazioni con masse minori. Saranno utilizzati inizialmente su auto ad alte prestazioni, ma si potrebbero diffondere in futuro come nuovo standard.
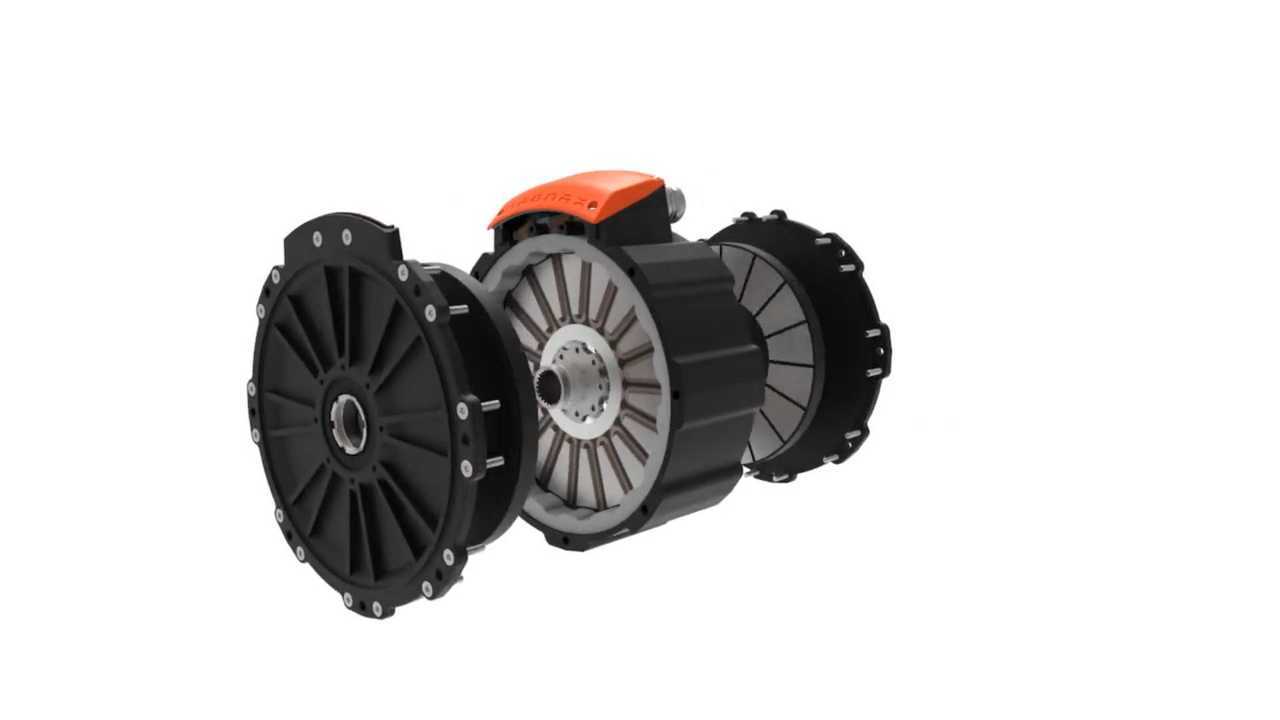
Il motore a flusso assiale yokeless Magnax promette un’efficienza del 98 percento
Ma quando le auto elettriche arriveranno ad avere un peso paragonabile a quelle con alimentazione endotermica? Le stime sono poco precise. Ma il fatto che si stiano facendo progressi evidenti farà perdere significato alla domanda. La cosa importante sarà avere auto elettriche efficienti, dotate di grandi autonomie e di prestazioni elevate, una volta raggiunti questi obiettivi, considerando l’andamento generale dell’industria automotive, il confronto con le auto a benzina non sarà più rilevante.
.
28/01/2023
fonte: INSIDEEVs
https://insideevs.it/news/633113/auto-elettriche-leggere-innovazioni-tecniche/